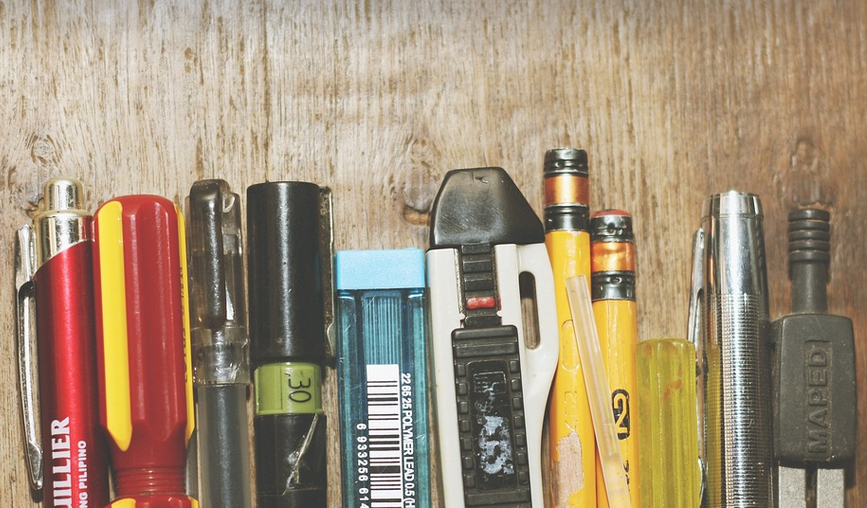
Understanding the Basics of Air Flow
When it comes to plasma cutters, we often hear about a crucial factor – airflow. But what exactly does CFM, or cubic feet per minute, mean in this context? Well, think of your plasma cutter as a tiny factory churning out metal-cutting magic. Airflow is like the conveyor belt powering that magic. A good amount of airflow ensures efficient cutting and prevents problems like sputtering or inconsistent cuts.
To truly understand CFM for plasma cutters, let’s break down how it relates to air movement. In simple terms, imagine a fan blowing air across a room. The more forceful the fan’s blow (meaning higher CFM), the greater the volume of air moving in that moment. Similarly, a plasma cutter uses compressed air to create a hot and ionized stream of gas that melts metal.
For this cutting process to work effectively, the air needs sufficient momentum to cut through the material, keeping the plasma torch at the right temperature to melt the metal.
Why CFM Matters for Plasma Cutting
The choice of a suitable CFM for your plasma cutter is critical. It directly impacts how efficiently and consistently you can cut various materials, from thin sheets to thicker plates and even heavy-duty steel. It also influences factors like:
- Cutting speed
- Heat dissipation
- Material thickness
- Torch life
- Quality of cuts
- Overall machine performance
Factors to Consider When Choosing CFM for your Plasma Cutter
Choosing the right CFM is like finding the perfect tool for a job. You need to consider various factors, including:
1. **Material Type and Thickness:** Plasma cutting different materials requires varying amounts of airflow. Thicker steel generally needs more airflow than thinner metals like aluminum or stainless steel.
2. **Cut Size and Complexity:** For intricate cuts or larger pieces, higher air flow is essential to ensure a smooth and consistent cut. For simple straight cuts on thinner material, lower CFM might be sufficient.
3. **Plasma System Technology and Power Output:** The type of plasma system you use also affects airflow requirements. Some systems are inherently more powerful and need less CFM than others.
How to Determine the Right CFM for your Plasma Cutter
So, how do you figure out the perfect airflow for your plasma cutter? Here’s a breakdown:
- **Consult Your Machine Manual:** This is the most crucial step. Your manufacturer will provide specific CFM recommendations based on their machine’s design and power capabilities.
- **Start Small and Adjust Gradually:** Begin by using a starting CFM recommended for your material type. Gradually increase airflow if necessary to achieve desired results.
- **Experiment with Different Settings:** Test out different airflows, paying attention to how the cut quality changes.
Tips and Tricks for Optimizing CFM
Once you’ve found a suitable starting point, here are some additional tips:
- **Maintain Clean Airflow Pathways:** Keep your torch tip clean and free of debris to ensure optimal airflow.
- **Check for Obstructions:** Regularly inspect your air intake and hose connections for any blockages or leaks that may hinder airflow.
Why Ask the Experts?
If you’re still unsure about the right CFM for your plasma cutter, reach out to a seasoned expert. The professionals at tool stores or welding equipment suppliers can offer personalized guidance based on your specific needs and budget.
Remember, choosing the right CFM is an essential step in achieving efficient and precise cuts with your plasma cutter. Understanding airflow and its relationship to performance will help you unlock your cutting potential.
Let me know if you’d like more information about a specific aspect of this guide!