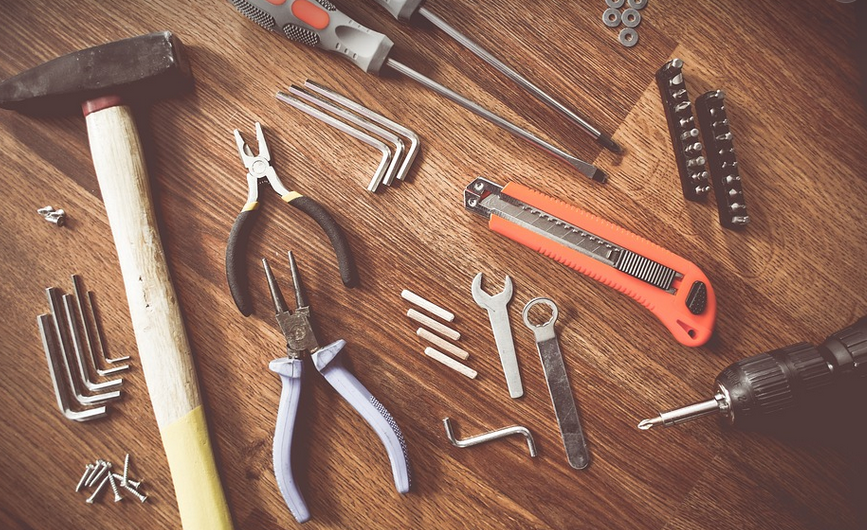
The Cornerstone of Quality: Understanding Tolerances in Plasma Cutting
In the world of precision metal fabrication, where intricate shapes meet the demands of modern manufacturing, CNC plasma cutting stands as a cornerstone. A tool that allows for incredibly precise cuts, it’s vital to understand and manage tolerances like a pro.
Why Tolerances Matter: More than Just a Number
Tolerances are numbers that dictate how much “play” exists between the intended shape of a cut and its actual execution. Think of them as a recipe for success in CNC plasma cutting. They ensure precision and accuracy, translating to flawless cuts that meet exacting specifications.
Imagine you’re building a custom motorcycle frame – the tolerances are critical. A slight difference in a cut can mean the frame won’t fit together right. This is why understanding the “real world” impact of these numbers is crucial.
The Anatomy of Tolerance: Unveiling the Different Types
There are two main types of tolerances in CNC plasma cutting:
- **Linear Tolerances:** These relate to straight-line measurements. Think of a cut that’s perfectly aligned for a specific part.
- **Angular Tolerances:** These describe the angle at which two lines meet. This is especially crucial in cuts where precise angles are needed
Beyond the Basics: Exploring the Factors Affecting Tolerances
Several factors influence tolerance values.
- **Material Thickness:** Thicker materials naturally require wider tolerances.
- **Cut Complexity:** A complex cut like a curved profile demands tighter tolerances than a simple straight cut
- **Machine Precision:** High-precision machines can achieve extremely tight tolerances.
- **Operator Skill and Experience**: The human element in cutting also plays a role, and consistent skill levels contribute to better execution.
- **Software Calibration**: Accurate software settings are vital for achieving the desired tolerance levels.
Embracing Precision: Measuring, Analyzing, and Optimizing Tolerances
To ensure smooth operation and high-quality cuts in CNC plasma cutting, these steps are essential:
- **Measure:** Before starting the cut, take detailed measurements. This helps establish a baseline for understanding what to expect from your machine.
- **Analyze**: After the cut, carefully examine and measure the resulting product to see if it’s within acceptable tolerances.
- **Optimize:** Use the insights gathered to fine-tune your process. Adjusting settings like cutting speed, amperage, and pressure can make a significant difference in achieving desired results.
The Power of Precision: Benefits of Tight Tolerances
Achieving tight tolerances isn’t just about aesthetics; it offers numerous practical benefits:
- **Increased Efficiency:** Minimal rework can save both time and money.
- **Improved Quality Control:** High precision leads to consistent, reliable parts.
- **Enhanced Product Life Cycle:** Well-made products that meet specifications will last longer.
- **Stronger Brand Reputation**: Customers trust businesses that deliver high-quality products.
The Future of Tolerances: Embracing Automation for Excellence
With the increasing demand for precision in manufacturing, CNC plasma cutting is evolving. Advanced automation technologies are enabling even tighter tolerances.
- **Machine Vision Systems**: These systems use cameras to detect and analyze part shapes, ensuring they meet specifications.
- **AI-Powered Optimization**: AI algorithms can learn from data and provide insights into process optimization, leading to more precise cuts.
Conclusion: Mastering the Art of Precision
CNC plasma cutting is a sophisticated technique that demands precision. By understanding tolerances and implementing effective measurement techniques, you can unlock the full potential of this technology to achieve exceptional results in your work. Remember, accuracy and consistency are key!